Purpose: This EarthCache is published by the
Connecticut Geological and Natural History Survey of the Department
of Environmental Protection. It is one in a series of
EarthCache sites designed to promote an understanding of the
geological and biological wealth of the State of Connecticut.
Supplies: You will need a copy of this login to
answer the questions once on site and be able to take a few photos
on site. Spoilers may be included in the descriptions or
links.
Location: N42 00.650 W 073° 17.530
Directions: The furnace is located on Lower Road,
East Canaan, CT. To reach the furnace, take Route 44 to East
Canaan, CT. Note the Canaan Congregational Church on the
south side of the road. Turn onto Lower Road.
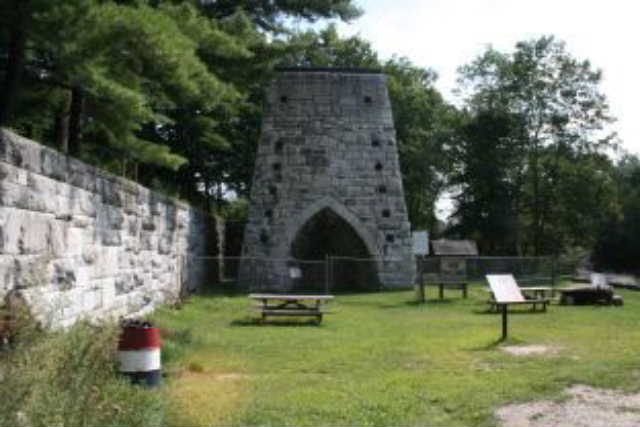
History of the Park: The Beckley Blast Furnace was
one of three blast furnaces in operation along Lower Road and the
Blackberry River in East Canaan during the period 1832-1923.
It was built in 1847 by John Adam Beckley, great-grandson of
Esquire Samuel Forbes and grandson of John Adam, Jr., founders of
the Forbes & Adam Iron Company. The Beckley Furnace (East
Canaan #2) produced pig iron until the winter of 1918-19.
Constructed of locally quarried marble, the furnace was originally
thirty-two feet in height and thirty feet square at the base.
Later the height was raised to forty feet making it one of the
largest of forty-three blast furnaces in the Salisbury Iron
District.
Beckley Furnace closed in the winter of 1919 at the conclusion
of World War I. After it’s closing the buildings and stack
slowly deteriorated. Then, in 1946, Civil Engineer Charles Rufus
Harte developed a plan for state purchase and preservation of
Beckley. In the process the Beckley Furnace was designated as
Connecticut's sole official state Industrial Monument and in 1978
Beckley was placed on the National Register of Historic Places.
The Process of Making Iron : Today it is very
difficult to find evidence of the industrial past of the Upper
Housationic Valley. More than 40 blast furnaces and foundries
took advantage of the co-location here of the key natural resources
needed to make iron (high grade iron ore, limestone, forests
to provide charcoal, and water power) and then to fabricate
products such as railroad wheels with the locally produced
iron.
Iron ore occurs in only five forms in Connecticut: as
magnetite deposits in rock, magnetite in beach placer deposits, as
limonite deposits in rock, limonite in bog iron, and as a carbonate
deposit. All are easy to purify
(smelt) simply by heating in a furnace with charcoal.
Chemically, it is a reduction reaction. Carbon from the
charcoal combines chemically with oxygen in the iron ore-mineral
releasing pure molten iron that collects at the bottom of the
furnace.
Bog ore. Iron is soluble when in a chemically
reduced form but is very insoluble when it is in an oxidized
form. Iron was dissolved from regional bedrock by reducing
ground waters. When the iron-bearing groundwater came to the
surface as springs that fed local bogs, the water oxidized
resulting in the precipitation of iron as the mineral limonite in
the bog sediments. Bog iron ore, in the form of rusty brown
lumps of low density, occurs in or near the surface of swamps fed
by springs carrying iron in solution. As such it is a
relatively recent deposit, having formed since the last Ice Age
(~17000 years ago). Mining bog iron ore was relatively
simple: scrape it up, wash off the mud, let dry then feed
directly into a furnace or forge.
Limonite ore (rock). Limonite deposited in the
local bedrock is denser and typically darker in color. In the
Salisbury District it is mixed with goethite, FeO(OH).
Mineralization occurred to rocks of the Walloomsac Schist
(Ordovician in age) near its contact with the underlying the
Stockbridge Marble (Cambrian in age). Mineralization probably
occurred during the last period of metamorphism in late Devonian
time. Mineralizing fluids dissolved iron from the schist and
were then transported until they were oxidized at or near the
contact with the marble. Mining the limonite rock ore
was also simple: most of it was taken from open pits where it
was dug, sometimes with the aid of blasting. The ore was
hauled by horse-drawn carts to where it was processed.
Smelting. Processing of the ore consisted of
crushing, removal of non-ore contaminants, and mixing with
marble. This mixture formed the charge that was loaded into
or near the top of the blast furnace with equal charges of
charcoal. The temperature achieved by burning the charcoal
was a function of the rate at which the oxidation reaction
occurred. Experience showed that maximum temperatures could
be achieved with a continuous supply of air blasted into the
furnace through ports near its base. In some cases the air
was pre-heated before being blown into the furnace. At the
same time the air was being pre-heated, water could be converted
into steam and used to power the air-blast machinery. The
blast furnace was essentially a large chimney with a slightly wider
portion about two-thirds of the way down. The wide portion
acted like a firebox. It narrowed toward the base where the
air-ports were located.
The charge, loaded into the fiery furnace, slowly worked its way
toward the bottom. Along the way the carbon in the charcoal
combined with the oxygen in the iron ore and escaped out the top of
the stack (chimney) as carbon dioxide and carbon monoxide.
The iron was left behind in a molten state and it collected at the
base in what was referred to as the “crucible”.
Impurities in the iron combined with calcium from the marble and
formed a lighter material referred to slag, which floated on top of
the iron in the crucible. Periodically the crucible was
tapped allowing the molten iron to flow out into channels dug into
wet sand outside the furnace. They were placed there to
collect the molten iron and allow it a place to cool and
solidify.
The 10-ton chunk of iron on display at this site formed in the
hearth area of the furnace. While there are a number of
things that can cause its formation this one was probably due to a
failure in the masonry of the hearth, which allowed the molten iron
to break through the side of the crucible. These chunks can
also form on the side of the furnace stack if the ore and limestone
were not properly loaded, clogging one or more of the tuyeres or
air ports, putting the fire out by preventing air from getting into
the furnace.
- What are these large single pieces of iron
called and how many of them have been discovered at this
site?
Drawing on the high quality ore from nearby Salisbury, marble
from local quarries and charcoal made from the surrounding hardwood
forests, the forges and furnaces of East Canaan played a major role
in the development of the nation’s iron industry.
The large crown gear resting near the upper section of the
stonewall drove the blowing engine to produce the required
airflow. Since Beckley was a hot blast furnace, the air
passed through a preheating over before being sent to the furnace
stack itself. The size and shape of the enclosure where the
turbine is now suggest that it originally held a water wheel.
The turbine must have been considered the latest in technology when
it replaced the water wheel. While waterpower was cheap and
clean it was not a reliable source of power.
- From the Turbine interpretive sign name two
of three reasons water caused the furnace to be shut down.
If you look over at the Blackberry River you will notice that
part of the river-bed flows over bedrock (ledge) and part of it
flows over sand and gravel that we refer to as alluvium. The
rock is composed of impure dolomitic marble that is relatively easy
to erode. Close to the shore of the river several curious
holes are found in the rock. These are referred to as
potholes. They are formed by abrasion of the rock localized
by swirling eddies in the stream bottom. Rock fragments and
sand grains are swirled by the water power and
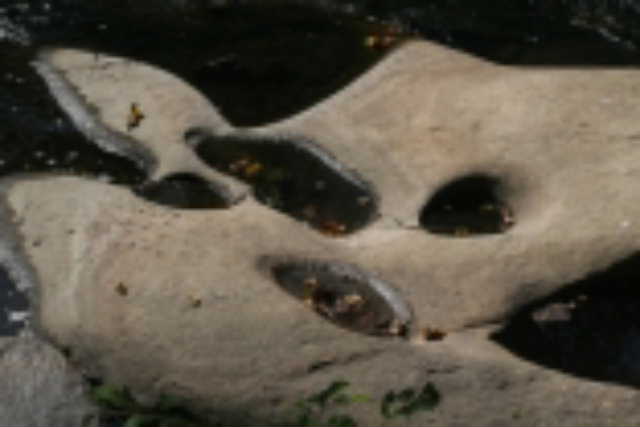
rub and smash against the rock, gradually drilling a hole in the
ledge. There are a number of small potholes at this site that are
mostly about 6” in diameter and up to a foot in depth.
A few are larger and a few are smaller. Potholes are known
from other sites that are a foot or more in diameter and 10’s
of feet in depth. These are just small puppies. Take
a picture showing at least two potholes from this
location.
To log this EarthCache: Answer the questions, and send a
photo at the site and number in group.
Footnote:
Historical Information provided by the Friends of the Beckley
Furnace, Inc.
Additional photos and information available at: http://www.betweenthelakes.com/
2-1bBq iron furnace slag heap P P P Yes Beckley Sate Historic
Site Northwestern Connecticut’s iron hills heritage an
analysis of restoration by: Jonathan Clapp
Images of America Connecticut Mining by John A. Pawloski,
(2006) Arcadia Publishing