History of Zinc
Zinc ores have been used in the making of brass and zinc compounds for over 2000 years, going back to the Romans who used zinc to make brass in the time of Augustus (20 B.C. - 14 A.D.). Later in the 13th century, Marco Polo described the manufacture of zinc oxide in Persia. By 1374, zinc was recognized in India as a new metal - the 8th metal known to man at that time. At Zawar, India, both zinc metal and zinc oxide were produced from the 12th to the 16th century. Zinc metal was used to make brass, and zinc oxide served medical purposes.
From India, zinc manufacturing moved to China in the 17th century where it developed as an industry to supply the needs of the brass industry.
Zinc was recognized in Europe as a separate metal in the 16th century when Georgius Agricola, a noted German scholar and scientist mentioned the formation of zincum, a new metal which was produced in the furnaces of Slesia. In 1743, the first European zinc smelter was established in Bristol in the United Kingdom using a vertical retort procedure.
A major technological improvement was achieved with the development of the horizontal retort process in Germany which led to the erection of smelting works in Slesia, Liege, Belgium and Aachen, the Rhineland and the Ruhr areas in Germany. In 1836 hot-dip galvanizing, the oldest anti-corrosion process, was introduced in France. Zinc production in the United States started in 1850.
For about 500 years zinc was produced from its oxide ores before the more abundant sulfides became the major source of supply. On the technological side, there was a drastic change in 1916 when the electrolytic process was introduced on a large scale replacing the pyrometallurgical process as the dominating production method.
Zinc is a natural component of the earth’s crust and an inherent part of our environment. Zinc is present not only in rock and soil, but also in air, water and the biosphere. Plants, animals and humans contain zinc.
Minerals and metals are mostly obtained from the earth’s crust. The average natural level of zinc in the earth’s crust is 70 mg/kg (dry weight), ranging between 10 and 300 mg/kg (Malle 1992).
In some areas, zinc has been concentrated to much higher levels by natural geological and geochemical processes (5-15% or 50,000-150,000 mg/kg). Such concentrations, found at the earth’s surface and underground, are being exploited as ore bodies.
Zinc Deposits
Zinc ore deposits are widely spread throughout the world. Zinc ores are extracted in more than 50 countries. China, Australia, Peru, Europe and Canada are the biggest zinc mining countries. Zinc is normally associated with lead and other metals including copper, gold and silver. There are four major types of zinc deposits:
1.Volcanic hosted massive sulphides (VMS)
VHMS deposits are polymetallic and are an important economic source of copper and zinc often associated with significant concentrations of silver, gold, cadmium, bismuth or tin.
2.Carbonate hosted (Mississippi Valley & Irish types)
Limestone and dolomite are the most common host rocks. The zinc lead content usually ranges from 5%-10% with zinc usually predominating over lead. Concentrations of copper, silver and barite of fluorite may also be present.
3.Sediment hosted (sedex deposits)
The host rocks are mainly shale, siltstone, and sandstone. Sedex deposits represent some of the world’s largest accumulations of zinc, lead and silver. The mineral has a high silver content. The lead/zinc content ranges from 10-20%.
4.Intrusion related (high sulphidation, skarn, manto, vein)
These deposits are typically found in carbonate rocks in conjunction with magmatic-hydrothermal systems and are characterized by mineral association of calcium and magnesium. Typically the ore body contains more lead than zinc and is associated with silver.
Zinc Minerals
The most commonly found zinc mineral is sphalerite (ZnS) also known as zinc blende, which is found in almost all currently mined zinc deposits. The mineral crystallizes from the hydrothermal solution as purezinc sulphide.
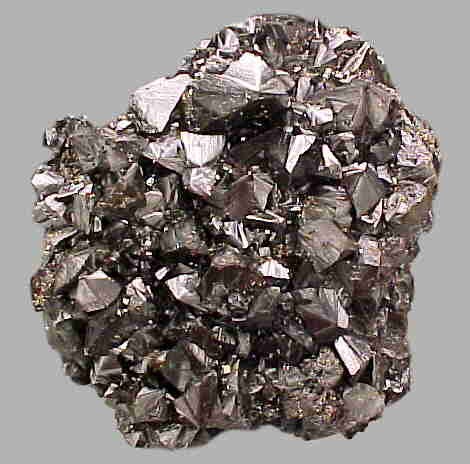
Sphalerite
The mineral marmatite is a complex zinc-iron sulphide, which is commonly found but rarely exploited as it is not easy to smelt.

Marmatite
Zinc deposits close to the earth’s surface are often converted to oxides and carbonates. Small quantities of zinc carbonate - the mineral calamine (smithsonite) in North America - often refer to the hydrated silicate mineral also known as hemimorphite.
Iron and lead sulphides, in the form of the minerals pyrite and galena are always associated in significant quantities while smaller quantities of other metals are commonly found.
Metamorphically formed oxide zinc ores such as franklinite or zincite are limited to only a few deposits.
Mining
80% of zinc mines are underground, 8% are of the open pit type and the remainder is a combination of both. However, in terms of production volume, open pit mines account for as much as 15%, underground mines produce 64% and 21% of mine production comes from the combined underground and open pit mining.
Rarely is the ore, as mined, rich enough to be used directly by smelters; it needs to be concentrated. Zinc ores contain 5-15% zinc. To concentrate the ore it is first crushed and then ground to enable optimal separation from the other minerals. Typically, a zinc concentrate contains about 55% of zinc with some copper, lead and iron. Zinc concentration is usually done at the mine site to keep transport costs to smelters as low as possible.
Roasting & Sintering
Over 95% of the world’s zinc is produced from zinc blende (ZnS). Apart from zinc the concentrate contains some 25-30% or more sulphur as well as different amounts of iron, lead and silver and other minerals. Before metallic zinc can be recovered, by using either hydrometallurgical or pyrometallurgical techniques, sulphur in the concentrate must be removed. This is done by roasting or sintering. The concentrate is brought to a temperature of more than 900°C where zinc sulphide (ZnS) converts into the more active zinc oxide (ZnO). At the same time sulphur reacts with oxygen giving out sulphur dioxide which subsequently is converted to sulphuric acid – an important commercial by-product.
The Hydrometallurgical Process
In a leaching stage the zinc oxide is separated from the other calcines. Sulphuric acid is used to do this. The zinc content dissolves whereas iron precipitates and lead and silver remain undissolved. However, the dissolved solution contains some impurities which need to be eliminated in order to obtain a high-purity zinc product at the end of the production process. Purification is mainly done by adding zinc dust to the solution. As all the elements to be removed lie below zinc in the electrochemical series they can be precipitated by cementation. The thus obtained purified solution passes an electrolytic process where the purified solution is electrolyzed between lead alloy anodes and aluminium cathodes. An electrical current is circulated through the electrolyte by applying an electrical difference of 3.3-3.5 volts between the anode and cathode causing the zinc to deposit on the aluminium cathodes in high purity. The deposited zinc is stripped off, dried, melted and cast into ingots. The zinc ingots may have different grades: High Grade (HG) 99.95% and Special High Grade (SHG) 99.99% of zinc.
Today over 90% zinc is produced hydrometallurgically in electrolytic plants.
The Pyrometallurgical Process
The Imperial Smelting process is based on the reduction of zinc and lead into metal with carbon in a specially designed Imperial Smelting furnace. The IS process is an energy-intensive process and thus became very expensive following the rise of energy prices. Today, Imperial Smelting furnaces are only in operation in China, India, Japan and Poland.
Current Zinc Uses
Currently over 11 million tons of zinc are produced annually worldwide. Fifty five percent of this amount is used for galvanizing to protect steel from corrosion. Approximately 17% goes into the production of zinc base alloys, mainly to supply the die casting industry and 12% to produce brass and bronze. Significant amounts are also utilized in rolled zinc applications including roofing, gutters and down-pipes. The remainder is consumed in compounds such as zinc oxide and zinc sulfate.
Historical Zinc Uses
Between 1874 and 1914, the Monumental Bronze Company of Bridgeport Connecticut started to manufacture zinc grave markers and larger monuments, calling their monuments "White Bronze". The sand cast zinc was produced and shipped around the world. It was less expensive and more durable when compared to more traditional stone monuments. Unfortunatly the cheaper cost was also part of the reason they fell out of popularity as many people felt it was not proper to remember a loved one with something that cost less. Zinc monuments are also a distinctive blue/gray colour which sets them apart from the rest of the monuments in a cemetary.
One of the advantages, besides the longevity and durability of the material, was that purchasers could select a general monument and customize all four sides if they wished, with a plate which was screwed to the headstone using decorative screws. The "Family" name was cast onto one side of the base in large block letters. The smaller, removable plates would normally have the name and age of the deceased, and their relationship to the head of the family.
After more then 130 years, every word and date is just as clear and legible as the day it was cast. The families who invested their money in these monuments certainly got what they were promised in terms of the superiority of the product to withstanding erosion from the elements.
Cleaning of these monuments was discouraged as the zinc headstones and monuments were meant to weather naturally so ionization of the metal would continue to build in the welds and make for a sturdier hold on all joints. However one weakness that has presented itself over time is that the pressure from the weight of the monument can cause the zinc plates to bend or creep outwards. This creeping action may also cause tiny cracks on some monuments.

Unstable contact with ground has caused bending of plates along lower base of monument.
There are a number of factors that can cause this creeping including the height and weight of a monument, and the sturdiness of the base where it contacts the ground. Proper seating on a solid base, ideally concrete, was important to reduce the creep and prevent corrosion from prolonged contact with the soils. Annual freezing and thawing of the ground can also cause shifting of the base of the monument unless it is on a solid or permanent base.

Creeping - Note the uneven contact with the ground
In an attempt to boost sales, the Monumental Bronze Company changed the "finish" on the metal base so it would resemble stone. The sandblasting roughened the surface and speeded up the natural formation of protective oxide coating. Many pre 1879 monuments are smooth with a grayish colour while the post 1879 monuments have rough surface and are more bluish-silver in colour.
The company ceased to cast memorials in 1914 when the plant was taken over by the U.S. Government for the wartime manufacture of gun mounts and munitions. The company officially ceased to exist in 1939 however company secretary C.A. Baldwin continued to cast the interchangable name plates for existing memorials.
To log this EarthCache:
Rules:
1. Park at the parking coordinates. There are designated spots to park and it is a short walk to the two monuments.
2. At the request of the property managment, do not take a photo of any monument that identifies family name. Photo's of a zinc monument that have the name obscured or show a decorative feature are fine. Photo's are not required to log this earthcache.
3. Please respect the opening and closing times of the cemetary which are from dawn to dusk.
Cache:
Visit two nearby zinc monuments (family name Phillips and Lick). Both monuments are of similar height and weight. Compare the two monuments and answer the following questions?
1. Feel the monuments base and describe whether they are smooth or rough to the touch?
2. Is it pre, or post 1879?
3. Compare the bottom base of each monument. Is there evidence of creeping or stress and if so, has one base held up better than the other base (Phillips or Lick)?
4. Hypothesize why there might be a difference between the stress evident on the base (if any) from one monument to the other monument?
Send me your answers to my profile. Do not post your answers on in your log.
Special thanks to bluegillfisherman for kindly allowing me to use some of his research and information from his EarthCache cache based in Indiana (GC1MJXA)

I have earned GSA's highest level: |
 |